
Puls Charging Bar device is utilized in industry for sticking materials to any surface or to each other. The sticking should be without any defects so then the materials are being unstuck, they should not damage the surface of the material. By utilizing Puls Charging Bar high resistant materials such as paper or plastic now can be easily clamped to surface. By using ionization system electrostatic charging generates the charger system by means of static generator and charging bar.
Charging bar is also designed to use charging in some quantity. Due to resistant connection to high voltage it does not emit a spark and enhances safety of work. Power supply voltage should be adjusted according to positive and negative polarity of charging bar. In sticking application charging bar should keep the distance to being charged materials in 10-20 mm.
Puls charging bar has an aperture behind, which by putting inside of it a plastic bar with M8 x 60 size, supplies simple and safe installation to any machine. To make static charge and sticking applications work properly it is necessary by using the most proper ionizing system to provide neutralization before two materials would be stuck to each other.(see Puls Static Elimination)
General Specifications
Easy to install / Resistively coupled / Spark-free
Applications
In mould labelling (IML) / Bags on roll / DVD manufacture / Board laminating / Compensating stackers / Film winding to roll cores / Flat bag with gusset / Multi sheet feeders / Side weld bag handles / Shrink wrapping / Electrostatic bonding
Technical Specification
Operating Voltage: Max. 20kV DC
Dimension: 31 mm x 40 mm
Construction: PVC
Ambient Temperature: 0 - 40ºC
Cable: 2 - 4 mt
Operating Distance: 10 - 20 mm
Mounting: M8 x 60 studs
Weight: 1,4 kg / mt
Lenght: Max 3940 mm
Polarity: N=Negative / P=Positive
Application
Extrusion Line Application Sheet
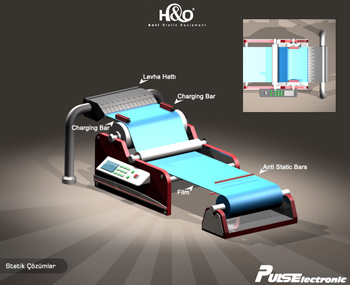
As the sheet exits the extruder head, it will start to generate a static charge as it cools. This is caused as the molecules rub against each other. As the charge increases, the electro-magnetic field will increase attracting airborne contamination onto the product.
The electro-magnetic field can also be absorbed into the bodies of operators working in close proximity to the extruder. The operator will then discharge (sometimes quite violently) when coming into contact with an earth potential such as a door handle, machine casing and another operator. Although the shock is painful but not life threatening, the involuntary reaction of the shock can be serious when the operator is working in close contact with working or moving machinery.
If you are using a chill roller to aid in the cooling of the product, a generator and charging head can be used to pin the edge of the sheet to the chill roller to prevent web wander.